Material is a Medium. It communicates ideas, beliefs, approaches: compels us to think, feel and act in certain ways; enables and enhances functionality and utility. Materials Experience emphasises this role of materials as being simultaneously technical and experiential.
Materials Experience Lab | Directed by Prof. Elvin Karana at Delft University of Technology and Prof. Valentina Rognoli at Politecnico di Milano.
About Us
Materials Experience Lab is a cross country research group bringing together researchers/practitioners who introduces unique ways of understanding and designing (with) materials to radically change and enhance the relationship people have with materials and artefacts. The Lab is committed to opening up new territories for material and product design and disseminate research findings through exhibitions, scientific publications, public debates, etc., with the aim of federating and supporting the research community (see, for example, the recent international conference, Alive. Active. Adaptive., that we organised under the Design Research Society (DRS) Special Interest Group on Experiential Knowledge (EKSIG 2017), http://www.eksig2017.com).
The main research activities of the Lab are coordinated by Elvin Karana and Valentina Rognoli. The core team consists of researchers/practitioners who actively work on a specific project under the Lab.
Our Approach
Our lab introduces unique ways of understanding and designing (with) materials by combining research methods, techniques, and tools from product design, social sciences, materials science, and engineering. The term ‘materials experience’ [1,2,3] describes our holistic view of materials in design, emphasising the role of materials as simultaneously technical and experiential.We believe that understanding material experiences, i.e. understanding how materials make us think, feel, and act, will provide new avenues to designing products and new materials.
Taking materials experience as an entry point, we create theories, tools and methods to: (1) understand and describe how people experience materials and how physical, biological, social, and cultural conditions constitute these experiences; and (2) inspire innovative material applications as well as new materials and design research trajectories. While most of our tools and theories are applicable in a variety of materials and design cases, in some projects we focus on specific materials, (3) to support emerging design practices urged by new and emerging materials.
In most of our research activities, we combine interpretive and empirical research techniques in a unique iterative manner, actively promoting a Do-It-Yourself (DIY) approach to materials [4] that pushes the boundaries of material (driven) design [5]. The DIY approach to materials brings people and materials closer in the making, promoting further consideration of contexts and time in designing, making, and use; greater awareness of the resources required; greater agency for working with materials; all of which leads to novel design outcomes.
History (by Elvin Karana)
My starting point was a simple observation: materials influence how products are embodied, how they function, and how they are experienced. They gratify or disturb our senses, they compel us to think, feel, and act in certain ways. These experiences influence purchase decisions and long-term satisfaction. Understanding materials as expressive as well as functional and structural entities not only invites but demands the proposition of new approaches to materials and design research and practice. Materials are a medium, a means in the designer’s hands, to communicate ideas, beliefs, and approaches. They are like words in a writer’s vocabulary. The designer needs to be sensitized to working with the material, in order to fully consider ‘what materials can do’, as well as we say in the lab ‘what materials want to be’.
In 2003 during my Masters’ studies, I saw there was no single systematic study providing an understanding of how we experience materials and how we can support product designers to involve such considerations in the design process. I and, later on, Bruna Petreca in textile and fashion design provided empirical evidence for this argument [6, 7]. To that end, Valentina Rognoli’s PhD thesis [8] has been a unique contribution to the domain providing a vocabulary and a tool for designers in understanding, communicating, and designing the expressive-sensorial qualities of materials and linking them to technical properties. Subsequently, my PhD thesis on Meanings of Materials [9] was the most elaborate study in product design at that time, providing empirical evidence on how we attribute meanings to materials and how we can support designers in understanding material-meaning interrelationships. Immediately after my PhD, my work attracted academic and industry attention, mostly material developers, who wanted to understand how their particular material could be received by consumers and how they could develop their material further to enhance consumer appreciation. Following this demand, my aim has been to operationalize materials experience thinking and suggest materials experience as a key entry point for materials and product development. Valentina and I have joined forces to promote this thinking among design and materials science communities over the last nine years.
Facilities
In the Netherlands, we have a DIY-Materials Lab, within the Applied Labs of the Faculty of Industrial Design Engineering-TU Delft and coordinated by the Emerging Materials research group. It consists of equipment for three main material themes: recycled, smart, and bio-based materials. We have a DIY hand-made machine for injection molding (designed by Dave Hakkens, https://davehakkens.nl), which can be easily operated by design students to tinker with plastics. We have a granulator from Zerma, an extruder and filament winder from Noztek. For designing (with) bio-based materials, we have sterilization equipment for tools and substrates (e.g. pressure cocker/autoclave); a flow box for working under a controlled environment and preventing sample contamination (e.g. for materials grown by micro-organisms, such as mycelium-based materials); a moisture chamber for growing/storing samples under controlled temperature and humidity conditions, as well as for testing moisture exposure; standard and vacuum ovens, as well as a high-temperature oven for ceramic materials; and a water-bath with controlled temperature range. On the technical characterization side, we have a universal testing machine for mechanical characterization (by Zwick /Roell) and a Dynamic Mechanic Analyzer (DMA). We have also access to the Applied Labs’ other machinery, such as multi-material 3D printers.
In Italy, our lab is named ‘The Materials Club’. This is a shared space between Polifactory (an interdepartmental research laboratory that explores the relationship between design and new digital manufacturing processes), the Materials Experience Lab, and the Polymers Engineering Lab of the Chemistry, Materials, and Chemical Engineering Departments “Giulio Natta” of Politecnico di Milano. At the Club, we can work on the same three central material themes as mentioned above and have another set of machines designed by Dave Hakkens, all the machinery required for rapid prototyping and making interactive devices. We have also the option to characterize DIY-materials created by design students in the chemistry lab.
Read more about Materials Experience Lab here:
http://www.materialstoday.com/lab-profile-elvin-karana-materials-experience-lab/
References
-
Karana, E., Hekkert, P., Kandachar, P. (2008) Materials experience: descriptive categories in material appraisals, The International Conference on Tools and Methods in Competitive Engineering (TMCE).
-
Karana E., Pedgley O., Rognoli V., (2014). Materials Experience: Fundamentals of Materials and Design, 1stEd., Butterworth-Heinemann: Elsevier, UK.
-
Giaccardi, E., Karana, E. (2015). Foundations of Materials Experience: An Approach for HCI. In Proceedings of CHI 2015. Seoul, South Korea. ACM Press: 2447-2456.
-
Rognoli, V., Bianchini, M., Maffei, S., Karana, E. (2015). DIY Materials. The Journal of Materials and Design, 86: 692-702.
-
Karana E., Barati, B., Rognoli V., Zeeuw Van Der Laan, A., (2015). Material Driven Design (MDD): A Method To Design For Material Experiences. International Journal of Design,9(2), 35-54.
-
Karana, E., Hekkert, P. & Kandachar, P., (2008). Material considerations in product design: A survey on crucial material aspects used by product designers. The Journal ofMaterials and Design, 29: p. 1081-1089.
-
Petreca, B. B. (2016) An understanding of embodied textile selection processes & a toolkit to support them, PhD Thesis, Royal College of Art.
-
Rognoli, V., Levi, M. (2005). Materiali per il design: espressività e sensorialità [Materials for design: Expressivity and sensoriality], PhD Thesis, Milano: Polipress.
-
Karana, E. (2009) Meanings of Materials, PhD thesis, Delft University of Technology.
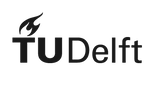
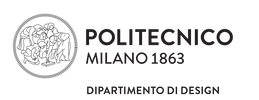